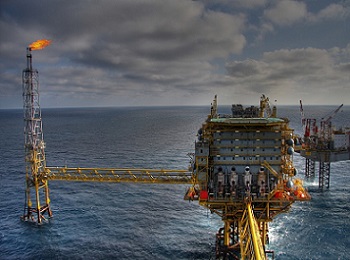
VINYL SYSTEM
Maybe it was forgotten?
Vinyl coatings have almost disappeared from painting cycles, especially in Europe.
Perhaps because they have not been shown to be valid over time?
The answer is no.
In contrast, they can still be considered one of the best organic coatings to applying onto steel. And that is why, to make “justice” to this type of product, Colgom wanted to do this short technical analysis.
The vinyl coatings are one-component, they drying by simple evaporation of the solvent; generally they are stainless, without odor, they do not feed combustion, mold and they are electrically neutral. Their advantages are toughness, flexibility and also ease and safety of maintenance.
They are made from copolymers, chloride and vinyl acetate dissolved in solvent. Their features vary according on the percentage of vinyl chloride present in the copolymer than to vinyl acetate. In some cases the copolymers are modified with a third component to obtain tripolymer products. These types of products allow the preparation of mixed vinyl-alkyd or vinyl-urethane paints which couple the characteristics of the two types of resin.
The former guarantee better durability and chemical resistance than alkyds, while the latter offer better resistance to temperatures and solvents than pure vinyls.
There are also epoxy-vinyl paints that are particularly interesting for the preparation of coats to connecting between epoxy and vinyl paints, but also polyurethane, polyacrylic and chlorinated rubber paints.
For applications on aluminum, hot-dip galvanized sheet and electrolytic, combinations with acrylic resins are particularly suitable: in fact, films characterized by high flexibility, excellent adherence and stability to aging are obtained.
CHARACTERISTICS OF APPLIED COATINGS
Operating temperature limits
Vinyl coatings are limited to an operating temperature of 70° C.
Resistance to abrasion and impact
They have good resistance to abrasion and impact.
Tenacity and flexibility
Generally they show a good hardness. However, all solvents to have evaporated from the paint before making these measurements.
Adhesion
Vinyl paints based on simple copolymers do not have a good direct adhesion on the sheet metal; in this case we need tripolymer resins, or other types of primers such as, for example, epoxy ones.
Retention of brilliance
The starting brilliance is less than that of conventional glazes, but the gloss retention is exceptional.
Chemical and corrosion resistance
Vinyl paints under normal operating conditions show excellent resistance to the most common inorganic acids, many organic acids and most gases. Excellent resistance to alkalis, salt solutions, alcohols and water. One of the most notable features is their resistance to a very long external exposure to the weather without alterations.
Compatibility with other cycles
The compatibility of a vinyl coat over the other one is one of the greatest advantages of vinyl paints when used as maintenance coatings. This is a feature that allows easy and inexpensive touch-ups and renewals. Most midcoats paints and vinyl finish coats adhere closely to the vinyl coat previously applied.
Aging and suitability for external exposure
Vinyl coatings are among the best in terms of resistance to aging, ultraviolet rays and external exposure. If properly pigmented, they do not become brittle, do not shrink, do not oxidize and do not change with aging or exposure to the elements. There are experiences of many years of exposure without alteration.
Possibility of maintenance
One of the advantages of the vinyl system is its ease of maintenance and safety. When at a certain period (durability) the protective system must be touched up or repainted, the solvent of the new vinyl paint softens the old one allowing the attachment of the new coats. The same happens when applying vinyl bonding coats on primer coats of different nature.
Composition of the production cycle
In the case of industrial protection (industrial and heavy atmosphere) of submerged structures, or marine atmosphere, the vinyl cycle can be composed as follows:
a) coat of anticorrosive vinyl or other types of primer such as epoxy
b) two or more intermediate or connecting vinyl coats
c) two or more coats of vinyl finish
Means of application
Vinyl coatings can be applied by spray, brush and roller.